Gas mass flow controller and vacuum pressure gauge in vacuum coating system
PVD, ALD: Control the flow and pressure in the vacuum coating system
Pressure fluctuations in the vacuum coating chamber will result in uneven coating and poor repeatability. While the mass flow controller controls the reaction gas, the pressure controller is used to control the pressure of the inert gas in the chamber, thereby improving the final plasma vapor deposition (PVD) results.
Fast, precise and stable pressure control in the vacuum coating chamber
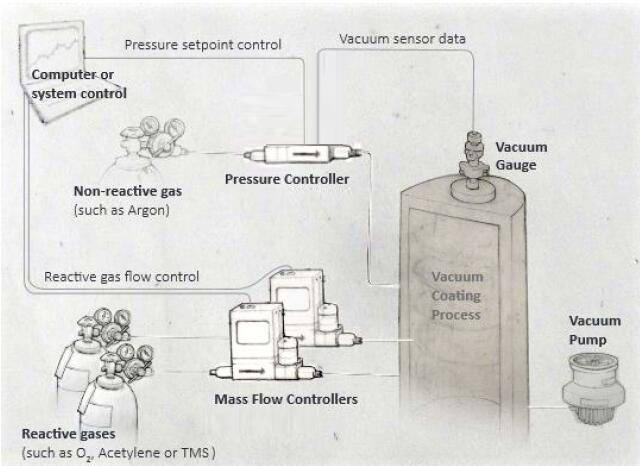
User pain points: the fluctuation of pressure in the vacuum chamber causes uneven coating and poor repeatability;
Problem description: The process of vacuum coating is usually carried out in a closed chamber with negative pressure. The reason why the vacuum is drawn is because the ambient gas will interfere with the reaction process between the various substances involved in the coating, and in a vacuum environment, the vaporized metal, ionized molecules, plasma reactive compounds and other coatings can be plated with other materials. Surfaces are fused.
To put it simply, a vacuum coating system usually consists of two main parts: the first is a vacuum chamber connected to a vacuum pump, and a throttle valve is usually used to adjust the vacuum level and control the shutdown to prevent leakage. The other part is the gas source. After passing through the mass flow controller, the gas is input into the vacuum chamber to form a gas density level suitable for coating. Some of them are non-reactive inert gases, which are only used to maintain the negative pressure environment of the vacuum chamber and will not have any effect on the concentration of the chemical substances involved in the reaction. Next comes the reactive gases, such as the oxygen used in the oxidation coating process. Some vacuum coating processes use a non-reactive gas as a carrier gas or dilute the reactive gas. The coating material may be a vaporized metal that is ionized by melting and electric field means. Some systems also have a portion of the "purging gas" used to "clean" the process chamber at the end of the reaction.
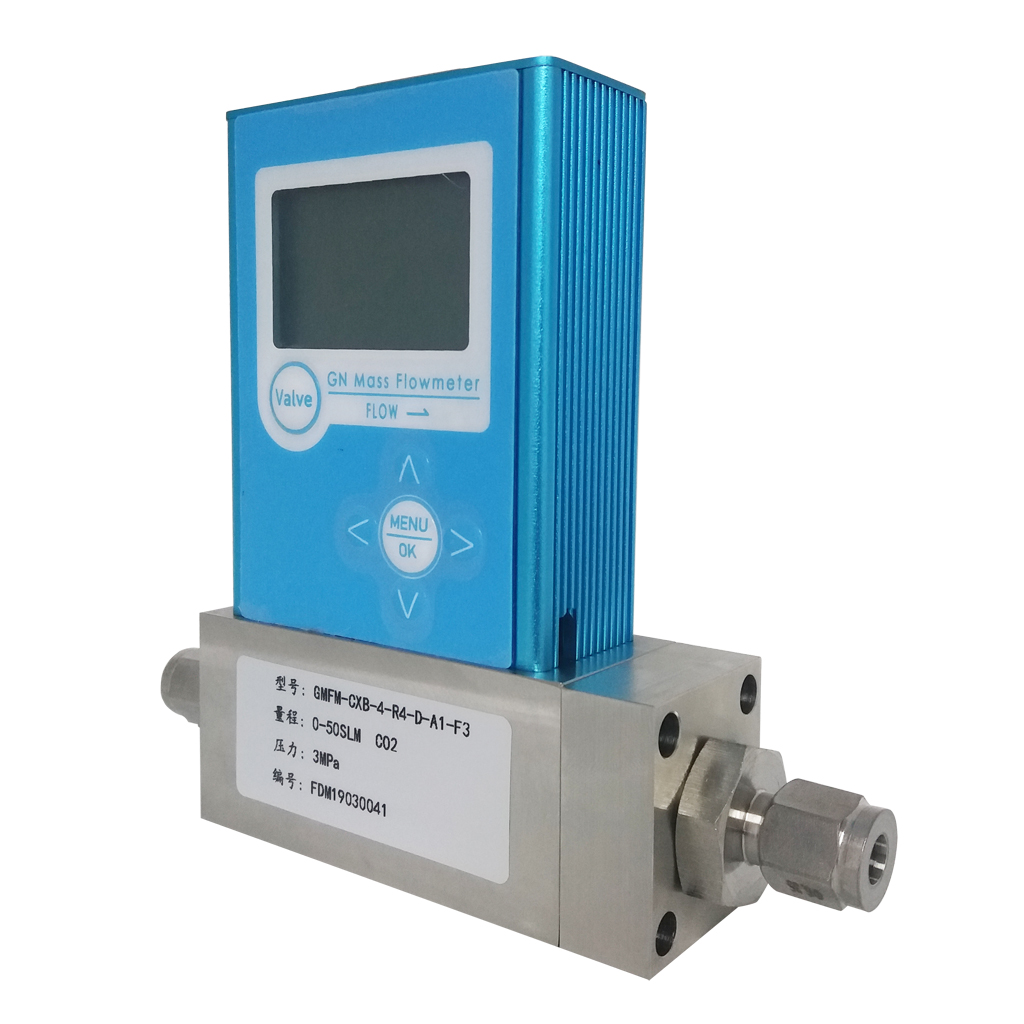
Coating principles are also varied. Some are relatively conservative, such as allowing the vaporized metal to slowly precipitate on the surface to be plated, while others contain a sol that fuses with the plated surface by forming a plasma vapor cloud arc, or charges the object to be plated to cause it to target the target. Ions generate adsorption.
In such thin-air environments, fluctuations in pressure are magnified, and a very small fluctuation can cause a series of butterfly effects. With the introduction of various inert gases and reactive gases, coupled with the start and stop of the vacuum pump, the interaction between various control components and the reaction of different time periods, all these will affect the pressure and balance of the entire process system.
More specifically, short-term pressure fluctuations caused by improper start and stop of the vacuum pump, or the long time taken for the mass flow controller that controls the intake air to reach the control point, these factors will make the delicate chemical balance in the vacuum reaction chamber invalid. , thereby affecting the uniformity, adhesion and thickness of the coating. Depending on the coating application, whether the control response time of the gas flow is within 100 milliseconds will essentially affect the thickness, uniformity, and repeatability of the entire coating process.
solution:
A vacuum gauge is used to control the pressure of the inert gas charged into the vacuum chamber to create a well-controlled coating environment. An external vacuum gauge connected directly to the reaction chamber measures the continuous process pressure, and this pressure reading is transmitted via an analog signal to the pressure controller and displayed.
The flow of the reacting gas into the cavity is controlled by a mass flow controller. Because the above-mentioned
pressure controller can measure the pressure in the cavity, and adjust the process pressure in real time by adjusting the content of non-reactive gases, so that the most favorable coating environment for deposition is formed in the cavity.
The fast control response speed is a crucial factor in reducing the pressure fluctuation in the cavity and forming the best deposition environment. Customized adjustment of the PID values of the mass flow controller and pressure controller according to the different process conditions in different applications, effectively eliminates overcharge, shortens the time to reach the set value, and controls the control response time within 20~30 milliseconds , thereby forming a stable pressure and gas exchange in the cavity.
The
mass flow controller of the small flow gas mass flowmeter (full scale 0.5sccm) is uniquely designed, with maximum flexibility, and provides customized pipeline interfaces and functions.
Program advantages:
Generally speaking, the change of reactive gas flow rate during vacuum coating will disturb the pressure in the reaction chamber, which will eventually lead to uneven and inconsistent coating.
While the mass flow controller separately controls various gases involved in the reaction in the cavity, the pressure controller precisely controls the pressure in the cavity within a specified range.
While the mass flow controller separately controls various gases involved in the reaction in the cavity, the pressure controller precisely controls the pressure in the cavity within a specified range.
According to the feedback from the vacuum coating system integrators using the above solutions, the Alicat mass flow controller and pressure controller with extremely fast response speed form a good coating environment through precise and stable control, Greatly improves the quality and repeatability of coating results.
If you want to know more about vacuum coating related information, and the industrial meters that need to be used, how to choose the model and what is the quotation, please contact winny han:sales01@cxflowmeter.com