Sharing of on-site installation guidance cases of liquid mass flow controller
Email: sales01@cxflowmeter.com
Whatsapp: 008618049841995
Case sharing:
The customer is a manufacturer of protein products (biomedical). The process requirement is to add a certain amount of methanol (±5% acceptable error) to the reactor
within a fixed time. If the amount of methanol is too little, the reaction will not be able to proceed. If the amount of methanol is too much, it will directly cause microbial
poisoning and cause the entire tank product to be wasted.
The customer placed the methanol tank in the distribution room on the first floor. By adding compressed air to the tank, the internal pressure of the tank was always
maintained at 0.25Mpa, and this pressure was also the power source for liquid transportation.
The liquid controller was installed on the production platform on the second floor. The length of the pipeline from the liquid tank to the controller was greater than 15m,
which caused the entire system to be unable to work at a constant pressure. The outlet pressure of the liquid tank was 0.25Mpa, and after passing through a 15m long
pipeline, it reached the front section of the flowmeter. The pressure was only 0.18Mpa, which could not meet the use requirements (the rear tank was 0.06Mpa constant
pressure), and the constant pressure of gas would cause untimely pressure replenishment (the pipeline was too long and the feedback was long) and the liquid would
be mixed with gas.
This resulted in unstable pressure pipelines with gas, and the controller could not accurately control it. The overall flow deviation is too large and there is no linearity.
On-site pipeline
Solution:
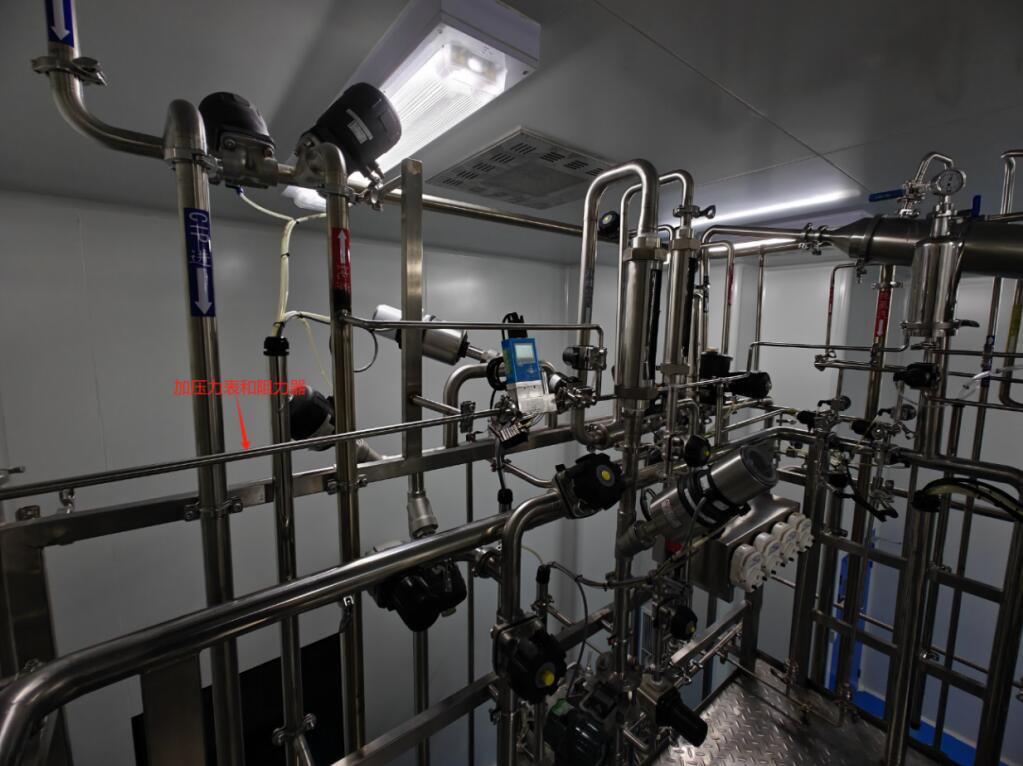
Increase the system pressure to ensure that the controller differential pressure meets the 0.2-0.3Mpa use requirement. Perform multiple calibration tests
under constant system pressure.
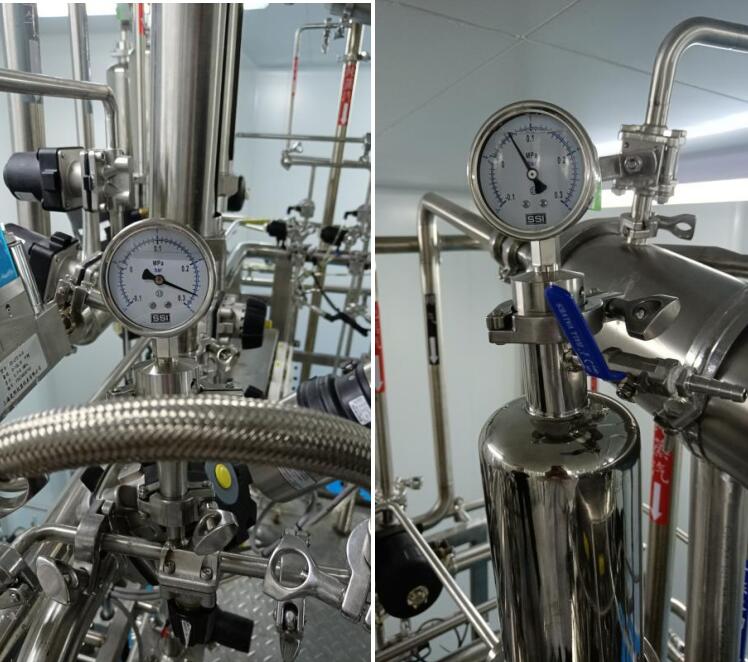
Email: sales01@cxflowmeter.com
Whatsapp: 008618049841995